Die Casting Tooling: Enhancing Business Efficiency
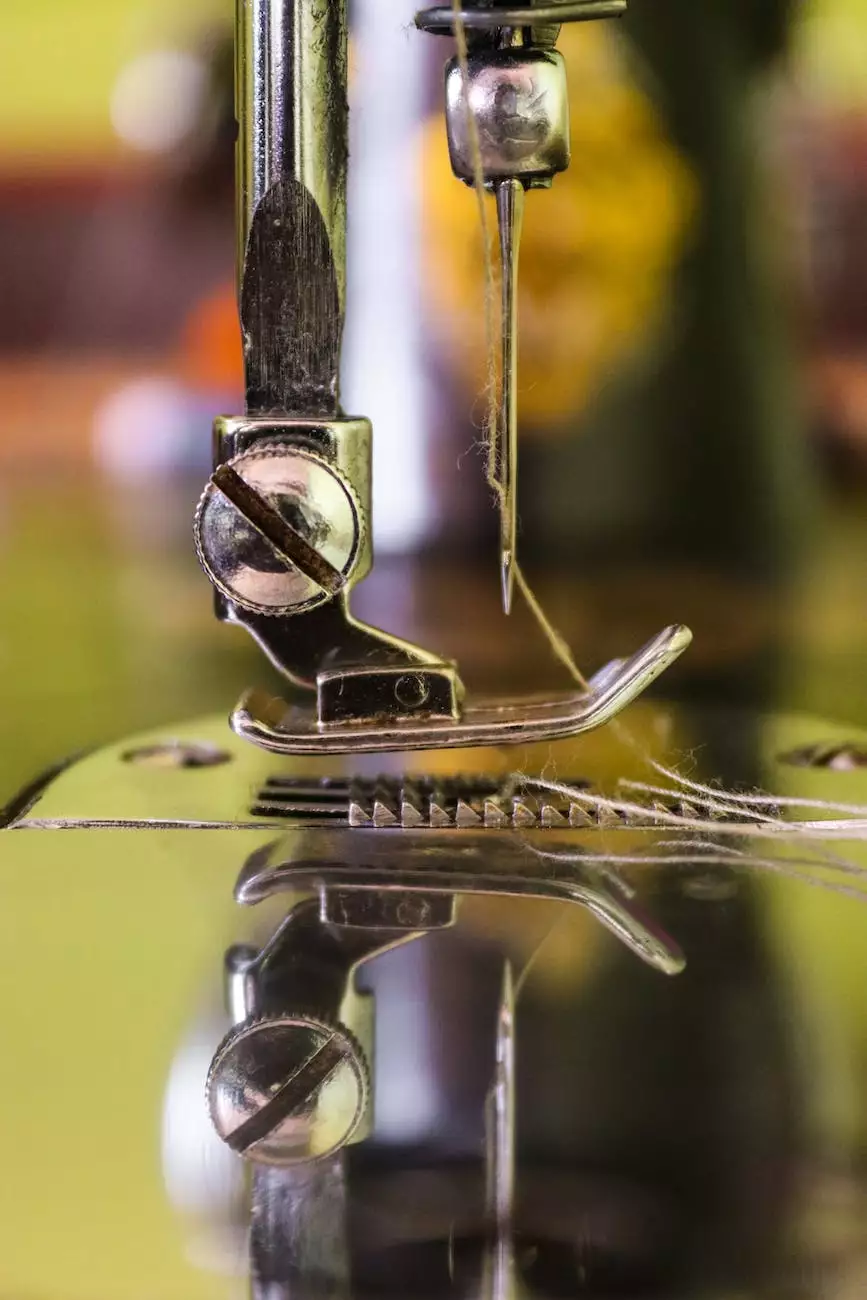
Introduction
As businesses strive to improve operational efficiency and maximize productivity, the manufacturing industry continues to evolve with innovative solutions. One such solution that has gained significant traction is die casting tooling. This advanced technique offers a multitude of benefits, including increased production speed, cost-effectiveness, and superior product quality. In this article, we will delve into the intricacies of die casting tooling and explore how it can transform your business operations.
Understanding Die Casting Tooling
Die casting tooling is a method used to produce intricate metal parts with high precision. It involves the use of reusable molds, known as dies, to shape molten metal into the desired form. This technique is widely employed in various industries, including automotive, aerospace, consumer electronics, and more. The die casting process offers exceptional detail, accuracy, and surface finish, making it an ideal choice for businesses seeking top-notch product manufacturing.
Benefits of Die Casting Tooling
1. Rapid Production: Die casting tooling enables high-speed production, allowing businesses to efficiently manufacture large quantities of products within short timeframes. This not only increases output but also ensures timely delivery to meet customer demands.
2. Cost-Effectiveness: By utilizing reusable dies, die casting tooling eliminates the need for constant mold replacements, significantly reducing production costs. Additionally, the high efficiency of the process minimizes waste, leading to further cost savings.
3. Enhanced Product Quality: Die casting tooling produces parts with exceptional precision, ensuring consistent quality and dimensional accuracy. The process eliminates variations often associated with other manufacturing methods, resulting in superior products that exceed customer expectations.
4. Wide Range of Designs: With die casting tooling, businesses can achieve intricate designs and complex geometries that are otherwise challenging to attain. This versatility opens up a world of creative possibilities, allowing for unique and innovative product development.
Implementing Die Casting Tooling in Your Business
Integrating die casting tooling into your business operations can be a game-changer, revolutionizing your manufacturing processes and driving overall growth. Here are some key steps to consider:
1. Assessing Your Manufacturing Needs
Begin by evaluating your production requirements and identifying areas where die casting tooling can bring the most significant benefits. Consider factors such as volume, complexity, and desired product characteristics. This analysis will help you determine whether die casting tooling aligns with your business goals.
2. Finding the Right Partner
To fully leverage the advantages of die casting tooling, it is crucial to collaborate with an experienced and reliable manufacturing partner. Look for a company with a proven track record in die casting, one that possesses the necessary expertise, state-of-the-art equipment, and a commitment to quality.
3. Designing and Prototyping
Work closely with your chosen partner to develop detailed designs and prototypes of your products. Through careful collaboration, you can optimize the manufacturing process, ensuring efficient die casting and minimizing potential challenges that may arise during production.
4. Production and Quality Control
Once the designs are finalized, the actual production process begins. Expert technicians will operate the die casting machinery, meticulously controlling crucial parameters such as temperature, pressure, and cycle time. Continuous quality control measures are implemented to guarantee that the finished products meet the highest industry standards.
5. Post-Production Finishing
After the parts are cast, additional processes such as machining, surface finishing, and assembly may be required based on the specific requirements of your products. These steps add the final touches to your parts, ensuring they are ready for distribution or integration into larger assemblies.
6. Continuous Improvement
To stay ahead of the competition and maintain the edge that die casting tooling offers, it is essential to foster a culture of continuous improvement within your organization. Regularly evaluate and refine your manufacturing processes, aim to optimize efficiency, and stay up-to-date with the latest advancements in die casting tooling technology.
Conclusion
Die casting tooling has emerged as a key solution for businesses seeking to enhance their manufacturing efficiency and produce superior-quality products. By leveraging this advanced technique, you can streamline your production processes, reduce costs, and achieve intricate designs that were once deemed challenging. Explore the possibilities that die casting tooling offers and partner with reputable experts who can help you transition into a more advanced and competitive future.