Understanding Peristaltic Pumps: Revolutionizing Industries
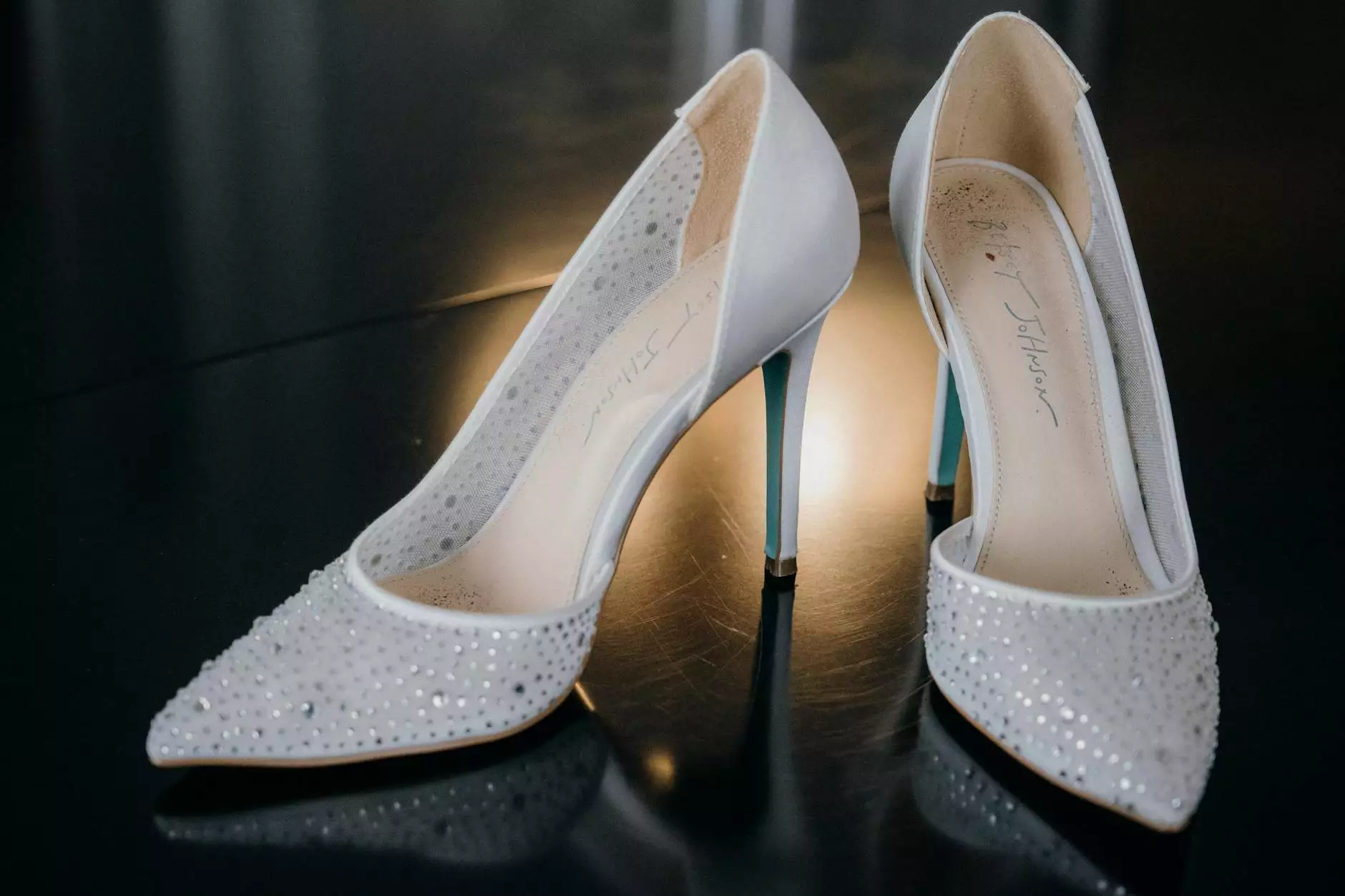
In the world of engineering and industrial applications, few technologies have proven as transformative as the peristaltic pump. This innovative device has captivated the attention of numerous industries due to its unique pumping mechanism and wide range of benefits.
What is a Peristaltic Pump?
A peristaltic pump is a type of positive displacement pump that moves fluids through a tube by compressing and relaxing the tube walls. The design of a peristaltic pump typically includes the following components:
- Hoses or Tubes: The medium through which the fluid flows.
- Rotating Rollers: These pinch the tube to create a vacuum that draws the fluid in.
- Motor: Provides the power to rotate the rollers.
- Chassis: The body that houses the components and maintains structural integrity.
This unique mechanism allows for a variety of applications across different fields, making peristaltic pumps essential equipment in modern engineering.
How Peristaltic Pumps Work
The operation of a peristaltic pump is fascinatingly simple yet highly effective. Here’s how it works:
- The motor drives the rollers, which move in a circular motion.
- As the rollers compress the flexible tube, a section is pinched closed, creating a vacuum.
- This vacuum draws the liquid into the tube from the fluid source.
- Once the rollers move past, the tube returns to its original shape, allowing the liquid to flow through.
Because of this operation, peristaltic pumps are ideal for handling various liquids, including corrosive and viscous fluids, without risk of contamination.
Advantages of Using Peristaltic Pumps
There are several key advantages to utilizing peristaltic pumps in industrial applications:
- Self-Priming: Peristaltic pumps can self-prime and are capable of running dry without damage.
- Versatile Fluid Handling: They can handle a range of fluid types, from shear-sensitive fluids to slurries.
- Simplicity in Maintenance: With few moving parts, maintenance is straightforward and cost-effective.
- Accurate Flow Control: Flow rates can be easily controlled by changing the speed of the rollers.
- Minimal Risk of Contamination: Since the fluid only contacts the tubing, there’s a reduced risk of contamination.
This combination of benefits makes peristaltic pumps an invaluable resource in various sectors.
Applications of Peristaltic Pumps Across Industries
The versatility of peristaltic pumps means they find use in numerous industries:
1. Pharmaceutical Industry
In the pharmaceutical sector, accuracy and cleanliness are paramount. Peristaltic pumps are used for dispensing medications, ensuring precise dosages without contamination.
2. Food and Beverage Industry
Food safety is critical; thus, peristaltic pumps are utilized for transferring fruit juices, dairy products, and other consumables, ensuring the integrity of the product.
3. Wastewater Treatment
In wastewater treatment, these pumps facilitate the transfer of sludge and various chemicals without clogging.
4. Chemical Processing
The chemical industry benefits from peristaltic pumps for mixing and transferring aggressive chemicals, as the pumps can handle high viscosities with ease.
5. Agriculture
In agricultural applications, peristaltic pumps are used for drip irrigation systems and fertilizer injection, providing efficient and precise delivery of nutrients to crops.
Choosing the Right Peristaltic Pump
When selecting a peristaltic pump, it's essential to consider several factors:
- Flow Rate: Assess the required flow rate for your application.
- Viscosity: Ensure the pump can manage the viscosity of the fluid being handled.
- Tubing Material: Select the appropriate tubing material based on chemical compatibility.
- Size and Space: Consider the spatial constraints of your setup.
- Power Requirements: Ensure the pump can operate with your existing power supply.
Challenges and Solutions in Using Peristaltic Pumps
While peristaltic pumps offer numerous advantages, there can be challenges:
1. Tube Wear and Replacement
The tubes used in peristaltic pumps can wear out due to repeated compression. It is essential to monitor tube condition and replace them regularly to ensure efficiency.
2. Temperature Sensitivity
Some tubing materials may not withstand high temperatures. Choosing the right material is critical for applications involving heat.
3. Bubble Formation
In some applications, especially when handling gases, bubble formation can disrupt flow. Proper system design can mitigate this issue.
The Future of Peristaltic Pumps in Engineering
As technology advances, peristaltic pumps are expected to incorporate smart technologies. Innovations may include:
- IoT Integration: Connecting pumps to the Internet of Things to monitor performance and maintenance in real-time.
- Energy Efficiency: Developing pumps with lower energy consumption can lead to more sustainable practices.
- Advanced Materials: Utilizing new materials can enhance pump durability and performance under extreme conditions.
These advancements will further solidify the position of peristaltic pumps as pivotal in various industries.
Conclusion
The significance of peristaltic pumps in modern engineering cannot be understated. Their unique design, versatility, and efficiency make them indispensable in a range of applications, from pharmaceuticals to agriculture. As we continue to innovate and improve these systems, the future looks bright for peristaltic pumps.
For those seeking not just equipment but comprehensive solutions in applications involving peristaltic pumps, Michael Smith Engineers stands ready to provide expert guidance and top-quality products tailored to your needs.