Custom Plastic Injection: A Game-Changer for Modern Manufacturing
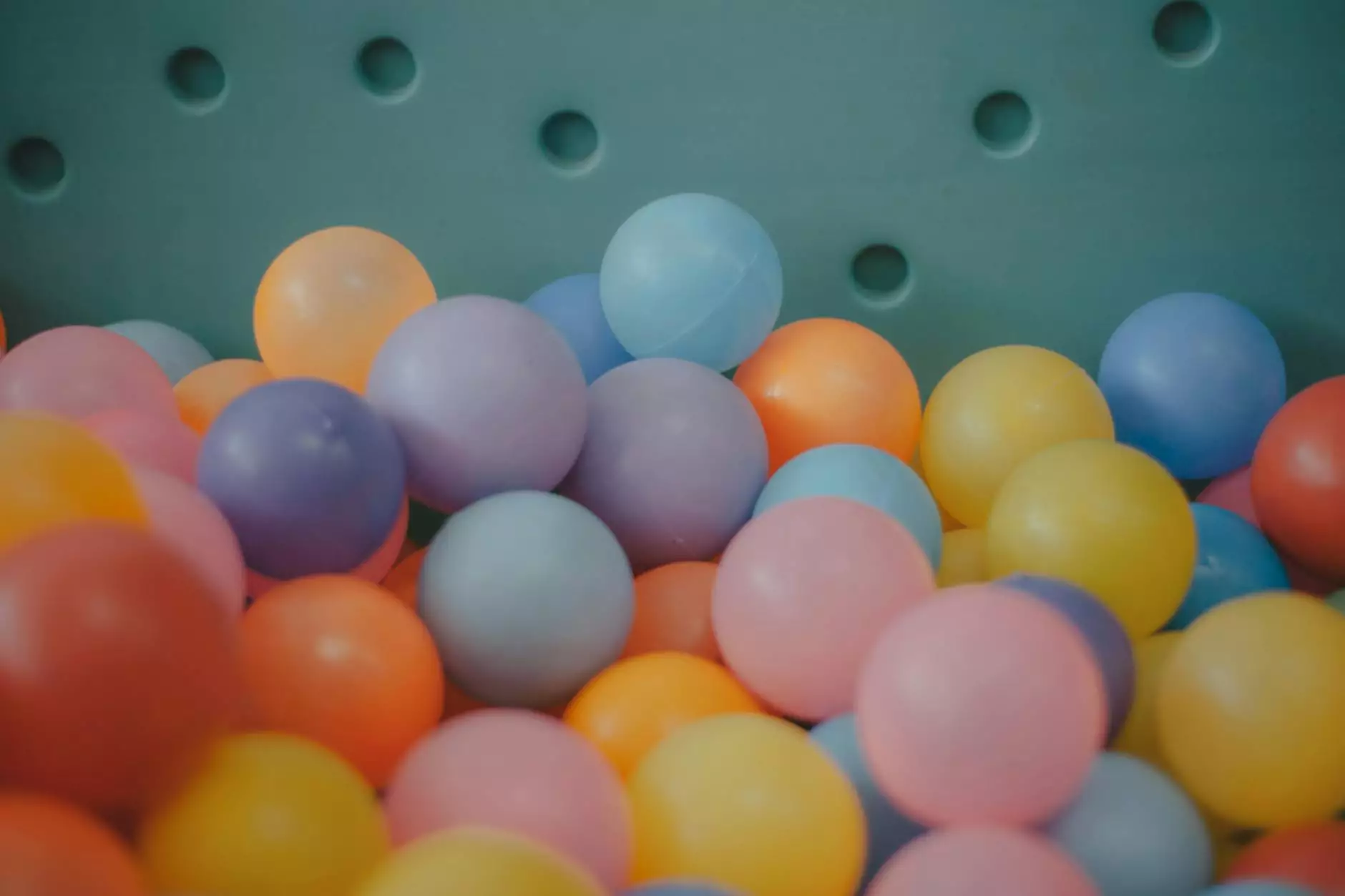
Understanding Custom Plastic Injection
Custom plastic injection is a sophisticated manufacturing process that allows for the mass production of highly precise plastic components. This technique utilizes a mold into which melted plastic is injected under pressure, resulting in parts that are consistent in quality and shape. Key industries benefiting from this process include automotive, consumer goods, and medical devices, where the requirement for precision and durability is paramount.
The Advantages of Custom Plastic Injection
One of the primary benefits of custom plastic injection is its ability to produce intricate designs that would be challenging or impossible to achieve with other manufacturing methods. Below are the key advantages:
- Cost-Effectiveness: Once the mold is created, the per-unit cost of production decreases significantly with higher volumes.
- High Precision: Molds are designed to deliver consistent results, ensuring each piece meets exact specifications.
- Material Versatility: A wide range of plastics can be used, opening avenues for numerous applications.
- Speed: Automated processes can produce large quantities of parts in a short amount of time, enhancing productivity.
- Low Waste: The efficient use of materials minimizes scrap and contributes to sustainability.
Applications of Custom Plastic Injection
With applications spanning numerous industries, custom plastic injection plays a pivotal role in modern manufacturing. Here are some prominent areas where this technology is beneficial:
1. Automotive Industry
The automotive sector relies heavily on custom plastic injection to produce critical components such as dashboard assemblies, bumpers, and lighting fixtures. The durability and lightweight nature of plastic parts contribute to fuel efficiency and safety.
2. Medical Devices
In the healthcare industry, custom plastic injection is essential for creating precision medical tools and devices. From syringes to complex diagnostic equipment, the reliability and hygiene of plastic components are crucial for patient safety.
3. Consumer Products
The consumer goods sector benefits from custom plastic injection by allowing for the mass production of household items, toys, and appliances. This method enables designers to market innovative products at competitive prices.
4. Electronics
Electronics manufacturers use custom plastic injection for enclosures and components that require careful engineering for functionality and aesthetic appeal. This method supports the rapid development needed in the tech industry.
Do-It-Yourself: Understanding the Custom Plastic Injection Process
To illustrate how custom plastic injection functions, let’s break down the process:
1. Designing the Mold
The first step involves designing a mold based on the required specifications of the end product. Engineers use computer-aided design (CAD) software to ensure precision.
2. Material Selection
Choosing the right type of plastic is crucial. Factors like strength, flexibility, and temperature resistance come into play, and engineers often select from a variety of thermoplastic and thermosetting polymers.
3. Injection
Once materials are prepared, they are heated until molten and injected into the mold. The applied pressure ensures that the plastic fills every cavity, capturing intricate details.
4. Cooling and Solidification
After injection, the material is cooled, causing it to solidify and take the shape of the mold. This stage is vital to achieve the desired dimensional accuracy.
5. Ejection
Once cooled, the finished product is ejected from the mold. If necessary, post-processing operations like trimming or assembly can follow immediately.
Quality Control in Custom Plastic Injection
Quality assurance is paramount in custom plastic injection. The manufacturers implement stringent quality control measures to ensure each part meets the required standards. This may include:
- Visual Inspections: Quick checks for visible defects.
- Dimensional Measurements: Utilizing tools like calipers and gauges to assess precision.
- Material Testing: Verifying properties of materials used in the production.
- Functional Testing: Assessing whether the part works as intended in its end application.
How Sumiparts Elevates Custom Plastic Injection Services
At Sumiparts, we pride ourselves on our expertise in custom plastic injection and other manufacturing methods such as machining, laser cutting, welding, and industrial supplies. Our commitment to quality and precision sets us apart in the industry. Here’s why you should choose us:
Expert Team
Our team comprises seasoned engineers and technicians who understand the intricacies of the custom plastic injection process and can guide you through every phase, from design to production.
State-of-the-Art Technology
We utilize the latest machinery and software in our production, ensuring cutting-edge solutions that enhance efficiency and minimize costs.
Tailored Solutions
We recognize that each project is unique. Our custom solutions cater to specific requirements, ensuring that we meet and exceed client expectations.
Sustainable Practices
At Sumiparts, we prioritize sustainability by minimizing waste in our custom plastic injection process and using eco-friendly materials wherever possible.
Future Trends in Custom Plastic Injection
The landscape of custom plastic injection is evolving rapidly. Here are some trends that are shaping the future:
1. Enhanced Automation
Automation is becoming increasingly important, allowing for faster production cycles and improved quality consistency. Smart factories initiated through Industry 4.0 principles will leverage IoT technology to monitor processes in real time.
2. Bio-Based Plastics
There is a growing push towards using biodegradable and bio-based plastics in the manufacturing process, aligning with global sustainability trends and consumer preferences.
3. 3D Printing Integration
While traditional custom plastic injection remains popular, integrating 3D printing for rapid prototyping allows for greater flexibility and speed in product development.
Conclusion: Elevating Your Business with Custom Plastic Injection
In today's competitive landscape, leveraging the advantages of custom plastic injection can significantly enhance your business operations. It not only streamlines production but also ensures high-quality output suited for diverse applications. Partnering with a reliable expert like Sumiparts enables you to harness this innovative technology to meet your manufacturing demands and achieve your business goals efficiently.
Explore our range of services including machining, laser cutting, welding, and industrial supplies to complement your custom plastic injection needs. Contact us today to discuss how we can help you optimize your manufacturing process and drive success in your industry.